在汽車研發(fā)過程中,為了保證汽車的技術(shù)特性、可靠性、耐久性和環(huán)境適應性,需要做大量的試驗。由于汽車需在不同的道路、地理和氣候條件下使用,它的性能、效率、可靠性和耐久性等不能只依靠計算,必須經(jīng)過試驗證實。在實際使用環(huán)境中、專用試驗場中或室內(nèi)試驗臺上,按照預定程序?qū)ζ嚮蚱淞悴考?、材料等進行的試驗。 今天小編為大家?guī)砹似囇邪l(fā)中需要做的試驗,這些試驗都是保證我們的車能安全、穩(wěn)定、可靠行駛的必要條件。主要包含以下內(nèi)容:整車試驗項目主要包含六大部分,他們是整車可靠性試驗、NVH試驗、HVAC試驗、EMC試驗、化學分析試驗以及整車道路性能試驗。接下來,我們逐一進行介紹下。整車可靠性試驗主要有環(huán)境適應性試驗、密封性能試驗、道路耐久性試驗、室內(nèi)模擬的碰撞和耐久試驗等。主要試驗項目如下:NVH是指Noise〔噪聲)、Vibration(振動)和Harshness〔聲振粗糙度),還包括汽車零部件由于振動引起的強度和壽命等問題。使乘員感受到的(聽覺、觸覺和視覺)是一種舒適的駕車或乘車環(huán)境。主要試驗項目如下:HVAC是Heating, Ventilation and Air Conditioning 的英文縮寫,就是供熱通風與空氣調(diào)節(jié)。HVAC試驗也就是供熱通風與空氣調(diào)節(jié)試驗,主要有排放與經(jīng)濟性、整車空調(diào)系統(tǒng)試驗、冷卻系統(tǒng)試驗、儀表校核試驗、溫度場試驗、耐候性試驗等試驗項目。主要項目如下:EMC測試又叫做電磁兼容(EMC),指的是對電子產(chǎn)品在電磁場方面干擾大?。‥MI)和抗干擾能力(EMS)的綜合評定,是產(chǎn)品質(zhì)量最重要的指標之一,電磁兼容的測量由測試場地和測試儀器組成。汽車EMC試驗主要試驗項目如下:化學分析試驗主要包括ELV整車拆解測試和整車VOC測試以及氣味評價。其中ELV測試是指汽車禁用物質(zhì)檢測,VOC測試是指整車揮發(fā)性有機物的檢測。整車道路性能試驗主要包括參數(shù)測量、檢查性試驗、磨合、滑行試驗、動力性試驗、燃油經(jīng)濟性試驗、制動性試驗、平順性試驗、操縱穩(wěn)定性試驗等內(nèi)容。主要試驗項目如下:DV是Design Verification,即設(shè)計驗證,此時可以是手工件或者模具件,在TG1數(shù)據(jù)凍結(jié)后開展,主要工作是對前期設(shè)計的結(jié)構(gòu)、材料、功能、性能等等進行綜合評估,同時暴漏設(shè)計過程中的問題點,并進行相應的整改來支持TG2數(shù)據(jù)的制作及后期模具件的開發(fā)。PV是Process Verification,即過程驗證,通常必須是正式的模具件,在TG2數(shù)據(jù)凍結(jié)后開展,主要工作是對產(chǎn)品的振動、“三高”的耐久、可靠性及穩(wěn)定性等進行驗證,是從供應商的量產(chǎn)生產(chǎn)線上做出來的零件。只有PV試驗通過之后的零件再完成PPAP審核,才具備量產(chǎn)供貨資格。在做試驗之前,首先要了解整車開發(fā)流程和零部件開發(fā)流程。主機廠有自己的整車開發(fā)流程,如下圖所示。對于全新開發(fā)的車型,通常要造三輪車(Mule Car、EP Car、OTS Car),對應的零件在搭載整車前都要進行相關(guān)的試驗,以滿足整車各階段交付物要求。通常在TG0數(shù)據(jù)凍結(jié)后即開展Mule Car的制作,此時的零件為手工樣件,在尺寸、性能方面可能和最終的開發(fā)狀態(tài)會有差異,但也需滿足一定的尺寸和功能要求,以支持Mule Car的整車相關(guān)試驗;而在EP Car 上大部分為軟模件,部分也可以是手工樣件,零件必須完成DV試驗才可搭載EP Car進行主要的性能、功能驗證工作,最后在OTS Car上必須搭載模具件,對應的零件需要完成PV試驗,以滿足整車最終的VTS要求。DV試驗通常在TG1數(shù)據(jù)凍結(jié)后進行,此時對應的主機廠對裝車的零件或系統(tǒng)進行設(shè)計狀態(tài)的結(jié)構(gòu)匹配、功能以及性能驗證,DV試驗的目的就是暴漏設(shè)計過程中的問題并進行相應的整改,對于開發(fā)件來講尤其重要,畢竟在TG1階段很多零件開發(fā)件只是做的手工樣件或者簡易的模具件,此時的結(jié)構(gòu)匹配,系統(tǒng)功能匹配以及性能表現(xiàn)都會與整車要求的實際狀態(tài)有差異,因此需要對零部件或總成進行DV試驗先對零件狀態(tài)做驗證,尤其對于整車法規(guī),安全等要求的零件狀態(tài)尤其重要。在DV試驗及相關(guān)整車試驗暴漏出的問題進行整改后,就可以開始進行TG2數(shù)據(jù)的制作,TG2數(shù)據(jù)需在整車開發(fā)流程中的G5閥點凍結(jié),在TG2數(shù)據(jù)凍結(jié)評審通過后方可以對設(shè)計的零件進行開模,故此階段的零件都是模具件,對應交樣的零件必須完成PV試驗,以支持OTS裝車進行驗證,整車耐久,振動等等一些列試驗驗收后,再進行PPAP認可。在主機廠TG1數(shù)據(jù)凍結(jié)并完成相關(guān)評審后,對DV試驗的內(nèi)容,要求,時間等進行DVP(Design Verification Plan)的編制,通常主機廠設(shè)計的零件的DVP由主機廠工程師來編制,而對于供應商設(shè)計的零部件通常叫黑匣子,必須由供應商來編寫,最終匯總在一個總表上,雙方完成會簽認可。主機廠會有各種整車級設(shè)計規(guī)范及試驗要求。試驗要求里面會具體體現(xiàn)試驗方法,試驗內(nèi)容,試驗設(shè)備,試驗次數(shù),驗收標準等等。同樣,供應商的各類試驗規(guī)范主要針對是零部件級別或者總成級別,根據(jù)位置不同,所處的整車環(huán)境不容,功能要求的不同試驗的項目和方法以及要求也會有區(qū)別。同樣,在主機廠TG2數(shù)據(jù)凍結(jié)并完成相關(guān)評審后,對PV試驗的內(nèi)容、要求、時間等進行PVP(Process Verification Plan)的編制。PVP的內(nèi)容更注重的是產(chǎn)品過程的驗證,為了滿足整車振動,耐久,可靠性等試驗,供應商對應的零件及總成需進行對應的可靠性試驗和環(huán)境試驗;其中可靠性試驗又包括老化試驗以及壽命試驗、環(huán)境試驗是指驗證產(chǎn)品環(huán)境適應能力的測試,比如高低溫存儲,高低溫耐久,高溫高濕耐久等。對于現(xiàn)成件或選型件來講,通常只需供應商提供一年內(nèi)的DV及PV試驗報告即可,當然,主機廠也會對一些關(guān)鍵零部件進行第三方試驗以驗證供應商提供的DV和PV試驗報告中的主要的功能及性能。對于開發(fā)件,為了降低開正式模具帶來的風險,通常在DV試驗階段也會進行部分的PV試驗,所以在DV試驗中會包含PV試驗,有些公司在整車開發(fā)流程時間上壓縮很緊,甚至可能直接開硬模,供應商的DV和PV試驗同時進行開展,而主機廠也直接在整車上來驗證,此做法的優(yōu)點是可以少造一輪車,壓縮了整車的開發(fā)流程,但由于直接開模正式模具,如果發(fā)現(xiàn)一些重大問題,那就適得其反,事倍功半了!(3) DV試驗側(cè)重于設(shè)計上的驗證,為滿足設(shè)計要求,通常需要細化到材料級別的試驗,在項目條目上比PV試驗多;而PV試驗側(cè)重于極端條件和工況下的振動耐久、可靠性、產(chǎn)品的穩(wěn)定性上等做評估,尤其耐久和可靠性試驗時間,相對DV試驗周期更長。(4) PV所做的試驗項目可比DV少,因為設(shè)計驗證試驗DV已經(jīng)把前期產(chǎn)品設(shè)計上的潛在問題已經(jīng)表現(xiàn)出來并進行過一輪或兩輪的整改,所以DV試驗是一份比較全面的試驗報告,一些主機廠要求細化到材料級別的試驗,尤其是內(nèi)外飾件對VOC,阻燃等有要求、從設(shè)計驗證開始就會對這些項目進行要求并驗證,而作為過程驗證試驗的PV,只針對這個過程生產(chǎn)的產(chǎn)品的性能的驗證。主機廠和供應商共同制定好DVP(或PVP)后更重要的工作就在于按照試驗計劃中的內(nèi)容、要求、時間嚴格執(zhí)行,如果不滿足相關(guān)要求,需要提出一系列整改措施,以滿足系統(tǒng)及整車的目標。不同的零件,尤其帶電件涉及到的項目可能更多(主要是功能性的需求多)。但不論是DV還是PV試驗,從試驗計劃的制定開始會涉及到很多的部門,尤其設(shè)計開發(fā)部門、試驗部門、以及整車性能部門和質(zhì)量部門等都需要參與到整個試驗過程當中。其中,設(shè)計開發(fā)部門負責DV試驗計劃發(fā)布、 試驗能力分析、 組織DV試驗和試驗過程管控,以及牽頭組織DV試驗的驗證評審等。性能部門牽頭進行DV試驗設(shè)計缺陷的質(zhì)量問題整改,協(xié)助試驗部門進行DV試驗計劃發(fā)布及 DV試驗開展、跟蹤,參與 DV試驗驗證評審,供應商能力考察等。質(zhì)量部門主要參與DV試驗全程質(zhì)量過程跟蹤,以及零部件、系統(tǒng)、整車性能及可靠性試驗驗證的最終評審驗收。 隨著CAE技術(shù)的進步,仿真分析同步在零件DV和PV試驗中。如早期的強度仿真,后期的整車約束系統(tǒng)仿真等。仿真可以指導零件性能的優(yōu)化方向,提前鎖定參數(shù)。針對較小改動,不用進行太多零件或整車的測試,而是用仿真來判斷風險大小,再確定是否有必要進行試驗。隨著自動駕駛的興起,自動駕駛在仿真測試的應用越來越多,接下來,就再給大家介紹下自動駕駛相關(guān)的仿真測試。自動駕駛系統(tǒng)測試不同于傳統(tǒng)的汽車整車或零部件試驗,更多的是參照軟件開發(fā)和測試的模型和流程。因此,我們首先要了解軟件開發(fā)的V模型。V模型是廣泛在軟件開發(fā)和測試中使用流程,V模型要求在開發(fā)團隊進行不同階段的開發(fā)同時,測試團隊編制對應的測試用例,并在開發(fā)階段完成后立即進行測試。這就要求在集成測試、系統(tǒng)測試等暫無完整產(chǎn)品樣件的情況下,就開始進行測試。在自動駕駛系統(tǒng)的開發(fā)過程中,越早發(fā)現(xiàn)問題則修正問題的成本越低。在開發(fā)的早期,就建立起測試驗證的手段,快速高效的發(fā)現(xiàn)和解決開發(fā)過程中的問題,可以有效減低開發(fā)成本、提高開發(fā)效率。根據(jù)RAND公司一份名為《Driving to Safety》的報告,要證明自動駕駛汽車相比于人類駕駛員能夠減少20%交通事故死亡率,需要進行約80億公里的公共道路測試,假設(shè)由100輛車組成的車隊每年365天每天24小時不間歇的以40km/h的平均速度進行測試,大概需要225年。 這個測試時間顯然是不現(xiàn)實的。就要求在實車測試之外,尋求其他的方法,大幅縮短測試時間。因此,在虛擬環(huán)境下進行大規(guī)模的仿真測試,成為了必須選擇的方法。針對自動駕駛系統(tǒng)測試,本部分主要通過仿真測試平臺搭建、仿真測試內(nèi)容和測試工具鏈三塊內(nèi)容給大家介紹。模擬仿真測試涉及到模擬場景的搭建,對照真實世界,仿真測試平臺由交通場景模塊、傳感器模塊、車輛動力學模塊和測試管理模塊構(gòu)成。如下圖所示: 交通場景模塊用于模擬車輛運行的外部世界。 一方面,模擬各種交通場景要素,比如:①高速公路、城市道路等不同的道路結(jié)構(gòu);②標志標線、護欄、交通燈等道路附屬設(shè)施;③轎車、卡車、摩托車、行人等交通參與者;④路障、錐桶、遺撒物等臨時物體;⑤晴、陰、雨、雪、白天、黑夜等不同的天氣。 另一方面,模擬不同交通場景要素之間的組合和動態(tài)關(guān)系,即不同的“場景”。比如:高速公路上,一輛轎車在被測車輛前方快速切入;十字路口黃燈時,一輛卡車在被測車輛前方緊急制動停車。 傳感器模塊用于模擬車輛上安裝的各種傳感器,從而獲得交通場景的狀態(tài)。一方面,根據(jù)傳感器種類的不同,模擬不同的信號內(nèi)容,比如:攝像頭傳感器輸出圖像信號,激光雷達傳感器輸出點云信號,導航傳感器輸出定位信號。另一方面,根據(jù)傳感器特性和參數(shù)的不同,模擬出其“局限”,比如:傳感器的探測范圍,攝像頭的畸變和炫光,不同材質(zhì)對激光雷達光線吸收的影響,護欄對毫米波雷達的雜波影響。車輛動力學模塊用于模擬車輛本身對自動駕駛算法控制的響應,特別是對加速、制動和轉(zhuǎn)向的響應。車輛動力學模塊一般參照真實車輛,由車身、動力傳動系統(tǒng)、懸架系統(tǒng)、轉(zhuǎn)向系統(tǒng)、制動系統(tǒng)和車輪等不同的子系統(tǒng)構(gòu)成。測試管理模塊,負責對以上三個部分組成的仿真測試環(huán)境的管理,保證仿真測試的效果和效率。一方面,對測試流程進行管理,比如:測試用例的選擇、測試的啟動和終止、仿真模塊的調(diào)度。另一方面,對測試數(shù)據(jù)進行管理,比如:測試用例的更新、測試數(shù)據(jù)的記錄和分析、測試報告的生成。基于模型的設(shè)計方法的不同階段,分別采用MIL/SIL/PIL/HIL等測試方法,有效的對嵌入式代碼進行測試和驗證。其中: MIL,Model in the Loop:模型在環(huán)測試; SIL,Software in the Loop:軟件在環(huán)測試; PIL,Processor in the Loop:處理器在環(huán)測試; HIL,Hardware in the Loop:硬件在環(huán)測試。 假設(shè)我們現(xiàn)在要開發(fā)一款AEB控制器: (1)MIL 假設(shè)我們已經(jīng)在支持MBD的工具(如Simulink)中,使用圖形化的方法開發(fā)出了AEB的算法,現(xiàn)在想要驗證該算法是否滿足要求,那么我們需要開發(fā)一個(或是有現(xiàn)成的其他工具)被控對象模型,在這里例子里是一個車輛模型。將控制算法和車輛模型連接起來,形成閉環(huán),并變換輸入和車輛模型狀態(tài),來對控制算法的功能進行測試。如下圖所示:
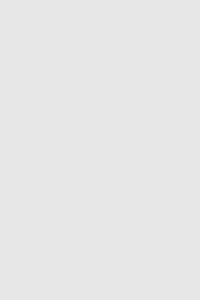
(2)SIL 現(xiàn)在我們將Simulink中開發(fā)的算法自動生成為c代碼。但是由于代碼自動生成工具本身的原因或者代碼生成工具沒有正確設(shè)置或者其他未知原因,自動生成代碼過程可能會引入一些錯誤。所以我們需要驗證自動生成的代碼與算法模型的一致性,這就是SIL測試。SIL測試使用與MIL相同的測試用例,查看對于相同的測試用例,查看其輸出是否與MIL階段一致。為了測試的高效性,有時甚至不接入被控對象模型,而是對算法模型和生成代碼進行相同的輸入,查看輸出是否一致。如下圖所示:
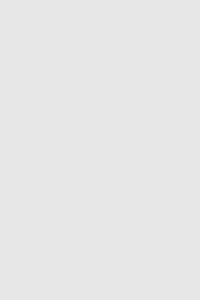
(3)PIL 將自動生成的代碼編譯為目標處理器需要的形式,并下載到目標處理運行,為了防止編譯過程引入新的錯誤,此時需要進行PIL測試。PIL測試也是等效性測試,其方式與SIL類似,不同之處是編譯好的算法運行在目標處理器上,SIL測試是在算法開發(fā)環(huán)境進行的(如windows)。 (4)HIL 在開發(fā)出完整的控制器后,有時被控對象(整車)還未完成開發(fā);有時使用真實被控對象進行測試太危險或成本高:出于這些不同的原因,采用真實控制控制器和虛擬被控對象的HIL測試常常被使用。如下圖所示:
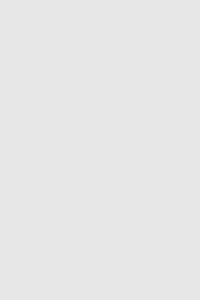
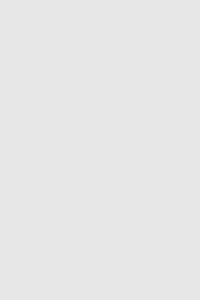 下圖可以整體看出自動駕駛系統(tǒng)分層測試的流程:根據(jù)自動駕駛中涉及的環(huán)境、傳感器、控制器和車輛四種元素的狀態(tài)的不同(是否用真實部件),仿真測試可以分為五個仿真級別。如下表所示。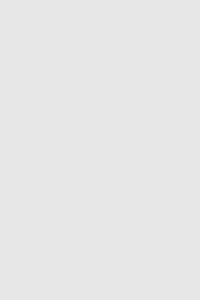
目前常見的仿真測試工具有很多種,根據(jù)自動駕駛開發(fā)團隊的來源,大致可分為如下幾個流派:傳統(tǒng)主機廠傾向于使用汽車工業(yè)的商業(yè)軟件,使用機器人平臺開發(fā)自動駕駛算法的團隊常常使用ROS/Gazebo,很多擅長計算機圖形學的團隊基于游戲引擎開發(fā)仿真工具。而大規(guī)模復雜交通流的仿真需求,則由交通規(guī)劃領(lǐng)域的軟件來滿足。 下圖列舉了一些常見的工具: 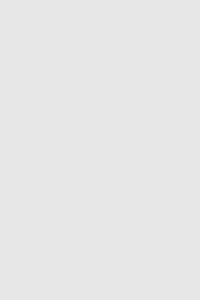
比如汽車工業(yè)的CarSim、CarMaker、VTD和PreScan,機器人開發(fā)的ROS和Gazebo,基于游戲引擎的CARLA、AirSim和LGSVL,以及交通規(guī)劃軟件VISSIM和SUMO。一個完整的、精度高的仿真測試平臺自然是最終的目標,但是在實際的自動駕駛開發(fā)中,團隊一定會根據(jù)當下的具體需求和成本限制進行選擇。 汽車大漫談:《零部件DV&PV試驗對比解讀!》天津汽車研究所:《汽車試驗:開發(fā)階段整車試驗項目匯總》程序員大本營:《自動駕駛虛擬仿真介紹1-7》
|